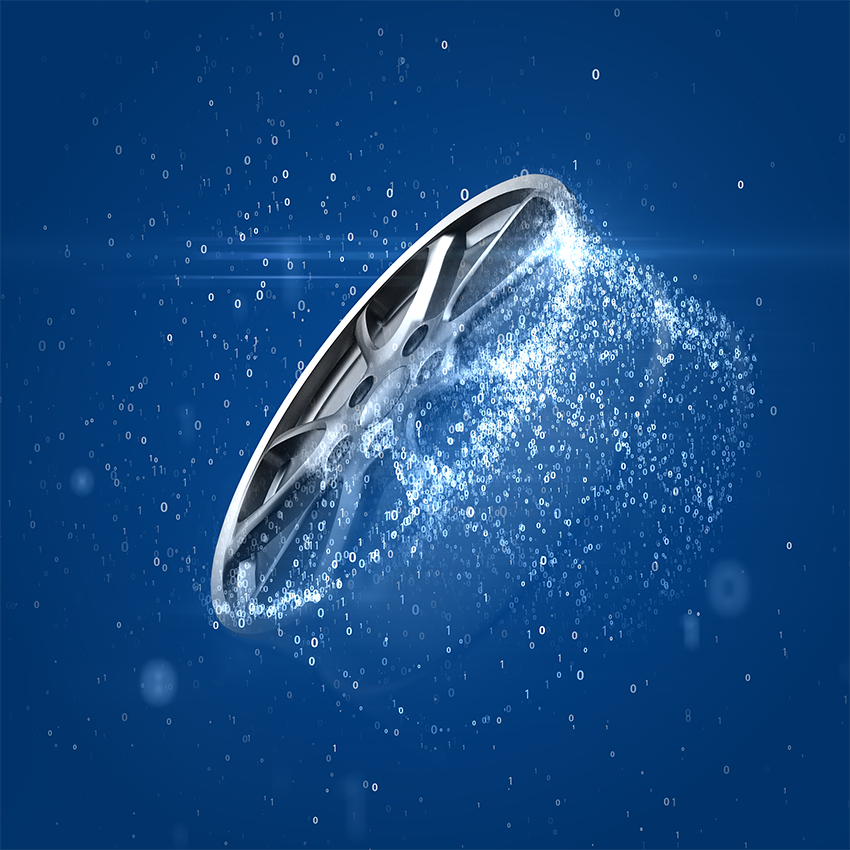
Optimizing the manufacturing process is one of the greatest challenges in the industrial production of components.
For components with high quality requirements, such as e.g. light metal castings in the automotive sector, a complete series test (inline test) with X-ray technology is common.
ISAR, our software solution for fully automatic inline X-ray inspection, offers all the important functions as a complete package. This includes both the fully automatic evaluation of X-ray images of the components with automatic defect recognition (ADR) and the monitoring of production.
ISAR has adapted image processing algorithms for 100% inline inspection for a wide variety of applications and manipulation systems. Here defect detection algorithms are employed that reliably detect standard defects, such as e.g. cavities and pores, as well as algorithms for special tasks (character recognition, low-contrast defects in wheels, etc.).
In addition, ISAR has a number of modules that allow optimal adaptation to the task and existing infrastructure. The focus here is on the seamless integration of testing into the entire production process. For example, creating a test program for light alloy wheels is simple and time-saving: a program for a new type of wheel is generated at a normal PC workstation and synchronized to all X-ray test systems in a plant or even across plants using a test program server.
Inline X-ray inspection cannot only ensure the quality of the components, it can also help to optimize the production process so that fewer rejects are produced. Deviations from the optimal production process are recognized early on and measures are taken to remedy these deviations. This is summarized under the term production monitoring. Less rejects lead to increased resource efficiency and thus to a reduction in costs.
Specially prepared test results are transmitted to production in real time and enable trend tracking and continuous optimization of the production process with the aim of minimizing rejects. The connection to existing operational data acquisition systems (DAQ) is therefore a matter of course.