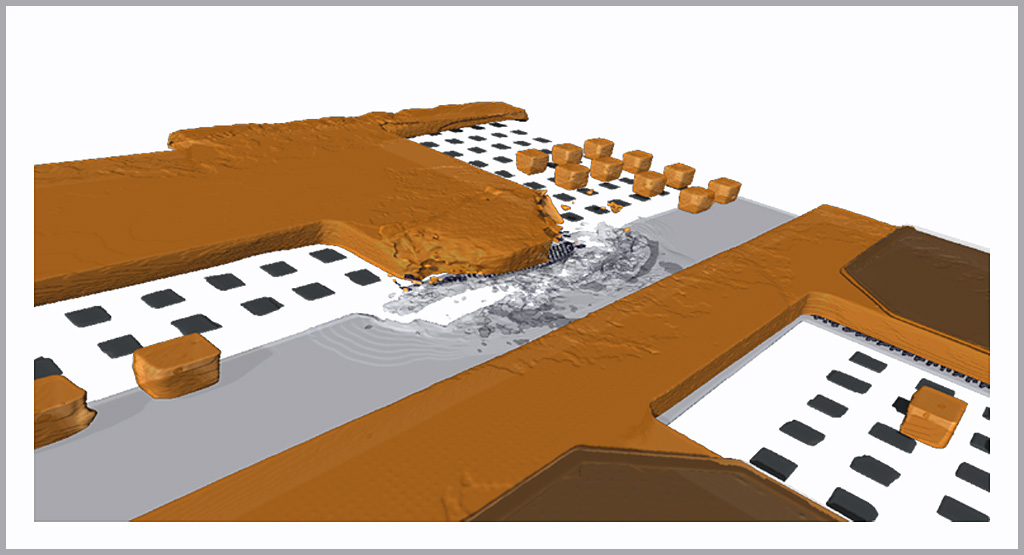
X-ray imaging helps with early detection of design weaknesses in semiconductors
Technical components are getting smaller and smaller, yet their performance is constantly increasing. Semiconductor components in particular – and especially those designed for automotive applications – are at risk of being exposed to strong current pulses. So as to ensure maximum failure safety and longevity even for such highly sophisticated components, manufacturers put prototypes through extensive testing prior to market launch.
Power temperature cycling tests are used, for example, to find out whether the components will continue to function reliably even under exceptional conditions. In these tests, the components are subjected to periodic voltage spikes, which result in temperature rises of several hundred degrees Celsius in very strongly delimited local areas.
Because of the complexity of the components, which are frequently made up of several layers, it is often difficult after a failure to draw conclusions about the exact course of events or the affected individual components. Furthermore, several failures usually occur in the moment of duress, the exact sequence of which is difficult to reconstruct and interpret.