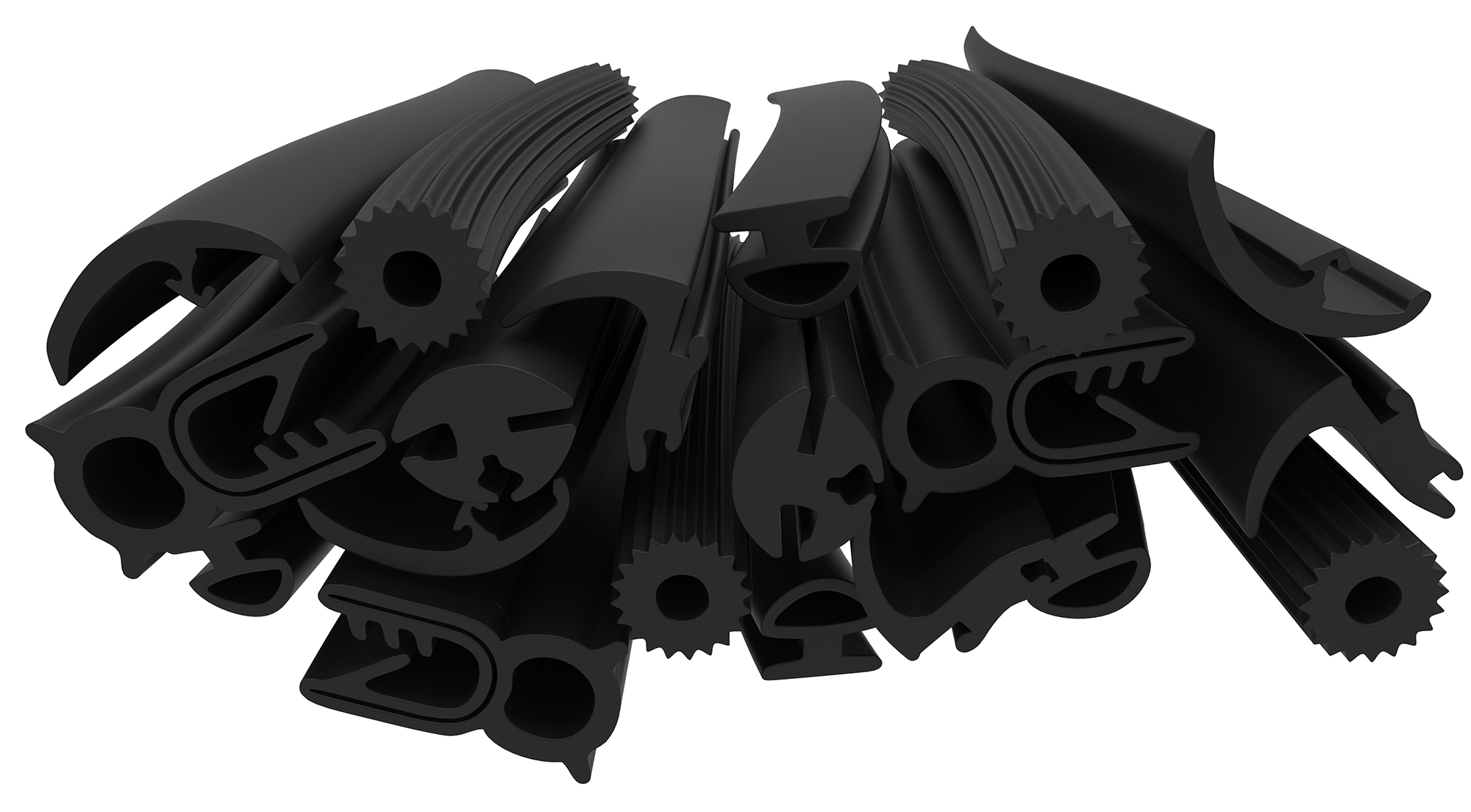
Produkte wie beispielsweise extrudierte Rohre, Schläuche, Profile und Dichtungen oder auch Schüttgüter wie zum Beispiel Kunststoff-Granulat werden »endlos« hergestellt. Die produktionsbegleitende Inline-Qualitätssicherung und –Prozessüberwachung solcher Produkte ist bisher unbefriedigend gelöst. Bisher wurden für die Detektion von Fehlstellen oder Maßabweichungen Methoden wie die Ultraschall-Prüfung und Terahertz-Prüfung eingesetzt – diese eignen sich jedoch nur für rotationssymmetrische oder flächige Objekte. Das Auflösungsvermögen ist wegen der relativ hohen Wellenlänge oft unzureichend. Optische Verfahren sind nur auf transparente Materialien oder Oberflächenmessungen beschränkt. Selbst Prüfsysteme, die an diese Spezialfälle angepasst sind, können lediglich lokale Messwerte und diese meist auch nur in Stichproben erfassen. Die Röntgen-Computertomographie (CT) ist zwar ein etabliertes Bildgebungsverfahren zur Qualitätssicherung und Diagnostik, jedoch sind bekannte CT-Systeme sehr komplex und für die Inline-Prüfung in kontinuierlichen Produktionsprozessen untauglich, da sie zu teuer, langsam und verschleißbehaftet sind. Ein System, das beliebige Querschnitts-Geometrien und Materialien vollumfänglich, zerstörungsfrei und kontinuierlich sowie mit hoher Auflösung und Geschwindigkeit überwachen kann, ist derzeit nicht am Markt existent. Ziel des Projekts TORERO ist es, diese Lücke zu schließen.
Im Projekt soll der Demonstrator eines neuartigen Röntgen-CT-Systems entstehen, das durch seine technischen und kommerziellen Kenndaten ein völlig neues Anwendungsgebiet erschließt. Es soll auf einen ringförmigen Detektor aufbauen, der mit einer Vielzahl ebenfalls ringförmig angeordneter, sequentiell operierender, gittergesteuerter Röntgenröhren kombiniert wird. Diese sollen gemeinsam um das Prüfobjekt rotieren und aus einem gemeinsamen Hochspannungsgenerator versorgt werden. Leistung und Energie der Röntgenstrahlung können dabei von der Steuerung individuell und schnell variiert werden. Die produktionsbedingte Vorschubbewegung bei der Schüttung erfolgt durch die beiden koaxial angeordneten Ringe hindurch. Die Vielzahl der Röhren erlaubt es, die Rotationsgeschwindigkeit vergleichsweise niedrig zu halten, was die Mechanik vereinfacht und den Verschleiß senkt, ohne die Vorschubgeschwindigkeit des Produkts zu limitieren. Elektronische Pulsung und mechanische Rotation überwinden den Nachteil rein stationärer Röhren-Arrays. Weitere Vorteile sind eine bessere räumliche Auflösung und ein gesteigerter Materialkontrast. Mit modernen Rekonstruktions-Algorithmen kann ein 3D-Scan des Produkts mit hoher Bildgebungsrate und Auflösung erstellt werden. Objekte lassen sich so nicht nur auf Fehler untersuchen, sondern auch dimensionell messen. Die Leistungsfähigkeit des CT-Konzepts soll anhand eines Dichtungsprofils aus der Automotive-Branche demonstriert werden.