Was ist der Sealinspector?
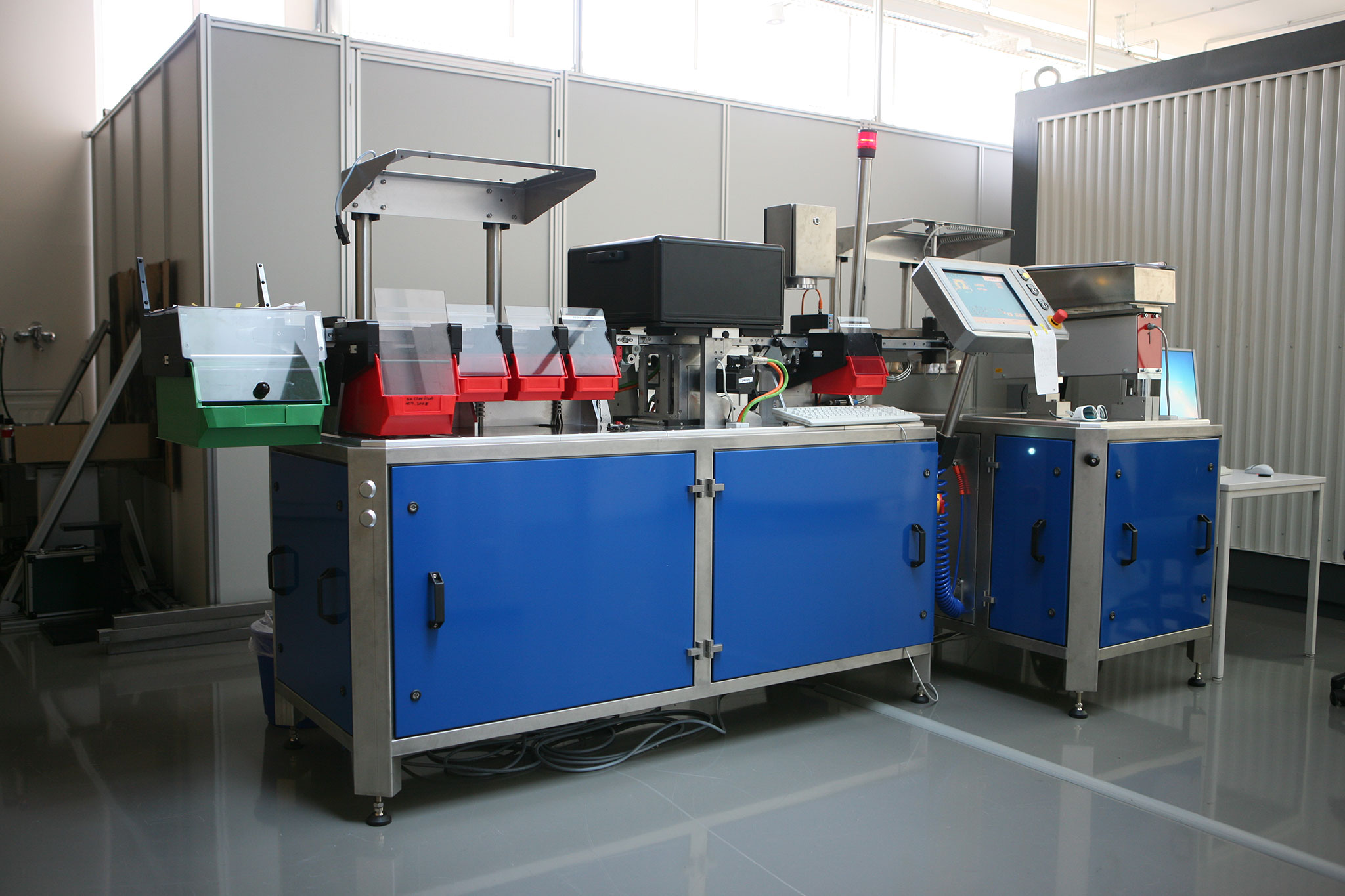
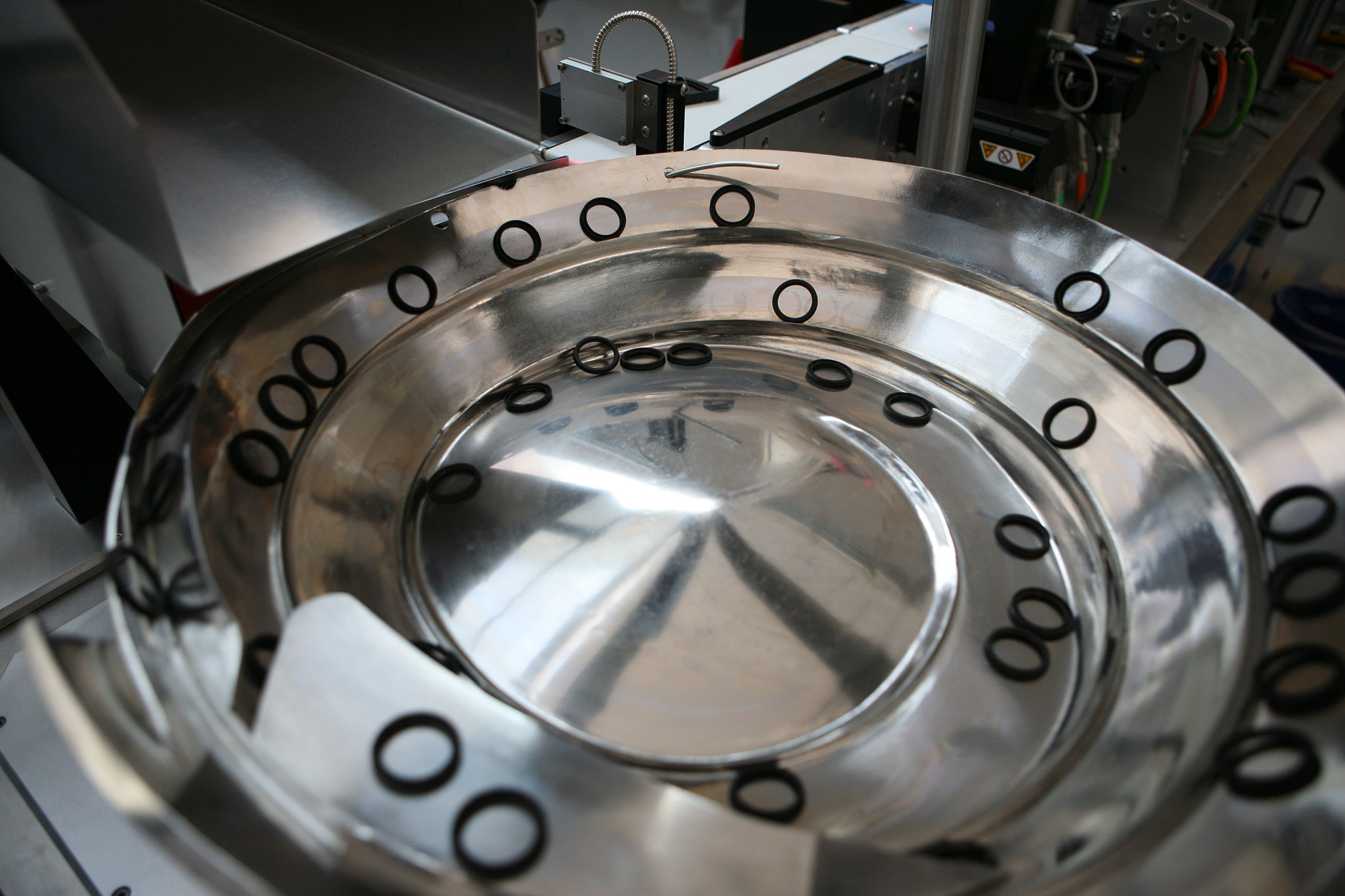
Der Sealinspector ist ein vollautomatisches System zur Prüfung von Polymerdichtringen. Polymer-Dichtringe spielen in vielen Bereichen unseres Lebens eine wichtige Rolle, insbesondere im Automobilbereich. Sie werden typischerweise im Spritzguss- oder Druckgussverfahren hergestellt. Da das Material durch mehrere Anspritzpunkte in die Form gelangt, kann es vorkommen, dass ein Anspritzpunkt verstopft ist und das Material von benachbarten Anspritzpunkten in diesen Teil der Gussform gelangen muss. So besteht die Gefahr, dass ein schwer detektierbarer Defekt entsteht. Aber auch Inhomogentitäten im Material können in der Anwendung zu Problemen führen. Bisher kommt oft noch die manuelle Inspektion zur Prüfung komplexer Dichtringe zum Einsatz. Gründe, die gegen eine manuelle Prüfung sprechen, sind beispielsweise kompliziertes Handling, riesige Prüfmengen und lange Prüfzeiten. Die effizienteste Lösung zur Prüfung von Massenware ist in allen Fällen ein vollautomatisches Prüfsystem, das auf die Prüfaufgabe maßgeschneidert ist. Nur so lässt sich eine zuverlässige Qualitätssicherung unter Berücksichtigung der wirtschaftlichen Aspekte erreichen. Das vollautomatische Prüfsystem SealInspector hilft, diese Fehler sicher festzustellen und ist eine Alternative zur aufwändigen und unsicheren manuellen Prüfung.
Die Entwicklung erfolgte in enger Kooperation zwischen Institut und einem Systemlieferanten. Die Systemkomponenten sind entlang eines zentralen Förderbands angeordnet, auf dem die Dichtringe transportiert werden. Zunächst werden die Ringe als Schüttgut in einem Vibrationsförderer vereinzelt und so auf dem Förderband abgelegt, dass stets dieselbe Seite nach oben zeigt. Danach wird die Oberfläche der Dichringe von allen Seiten dreidimensional erfasst. Nach der Auswertung der so gewonnenen Daten, werden potenziell defekte Dichtringe mittels Druckluft aus dem Produktionsstrom entfernt und in Behältern zur möglichen Nachkontrolle gesammelt. In einem Behälter am Ende des Förderbands werden die Dichtringe aufgefangen, die alle Kontrollen bestanden haben.