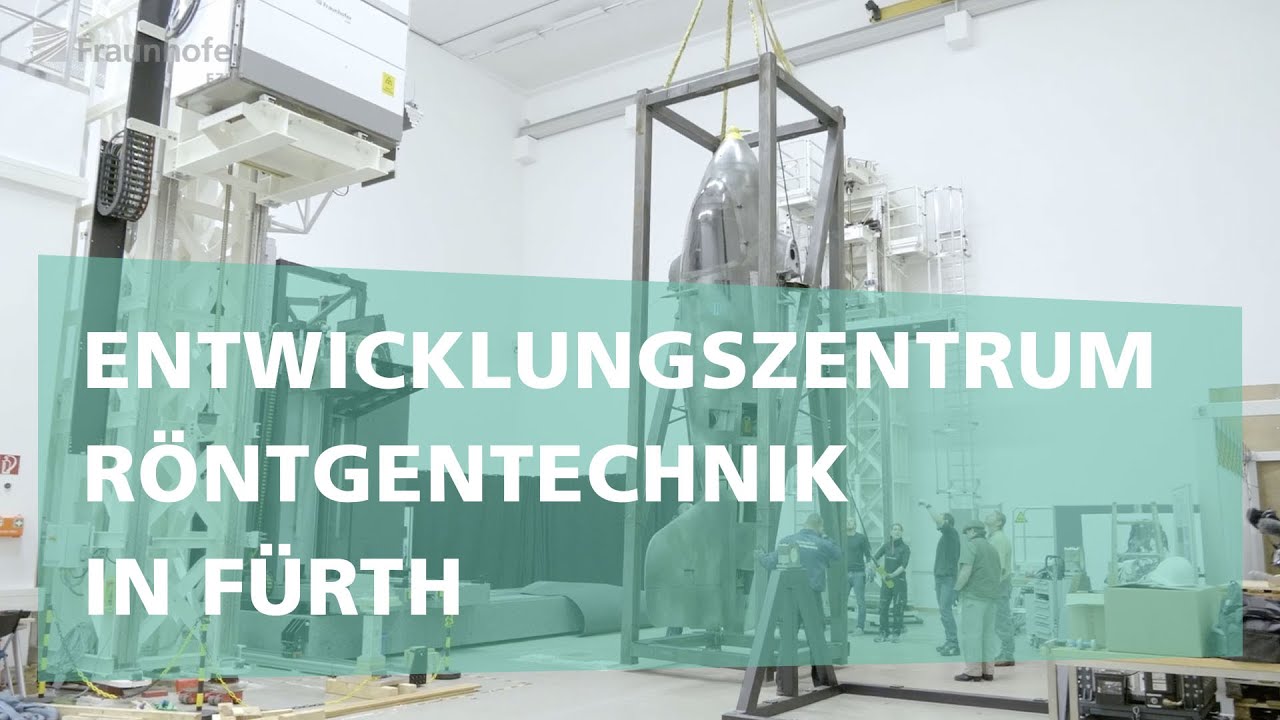
Datenschutz und Datenverarbeitung
Wir setzen zum Einbinden von Videos den Anbieter YouTube ein. Wie die meisten Websites verwendet YouTube Cookies, um Informationen über die Besucher ihrer Internetseite zu sammeln. Wenn Sie das Video starten, könnte dies Datenverarbeitungsvorgänge auslösen. Darauf haben wir keinen Einfluss. Weitere Informationen über Datenschutz bei YouTube finden Sie in deren Datenschutzerklärung unter: https://policies.google.com/privacyAm Standort Fürth forschen und entwickeln in enger Zusammenarbeit die Abteilungen »Anwendungsspezifische Methoden und Systeme«, »Produktionsmonitoring« und »Berührungslose Mess- und Prüfsysteme«. Durch unser einzigartiges Know-how auf dem Gebiet der zerstörungsfreien Prüfung können wir für nahezu jede Problemstellung die passende Lösung anbieten.
Neben exzellentem Fachwissen verfügt der Standort Fürth auch über hervorragende technische Ausstattung. Es stehen nicht nur zahlreiche Röntgensysteme für verschiedenste Aufgabenstellungen zur Verfügung – an das Entwicklungszentrum Röntgentechnik ist eine europaweit einzigartige Testhalle angeschlossen, in der sich komplette Fahrzeuge scannen lassen.